Tech
Most Noteworthy Advantages to Using Plastic Injection Molding for the Manufacturing of Parts
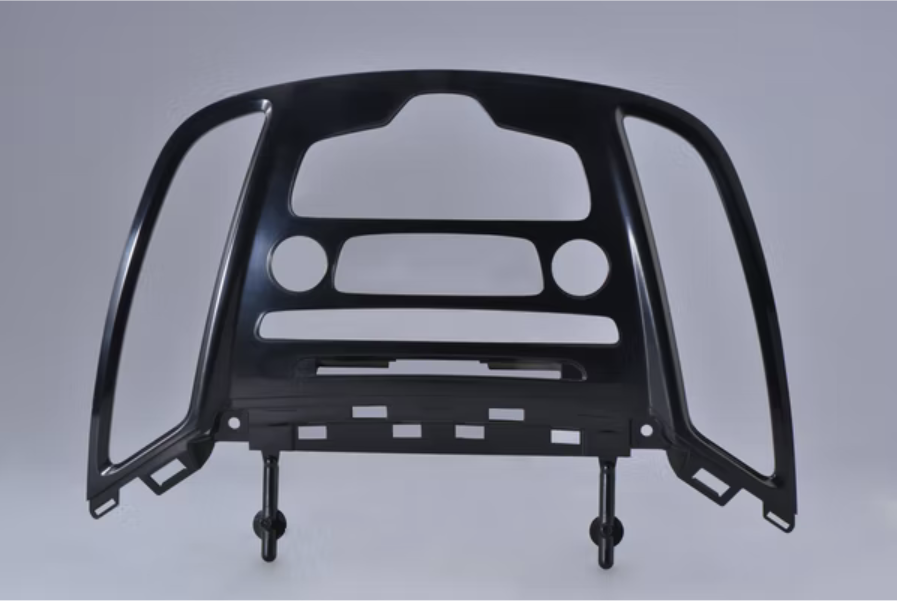
Injection molding is a manufacturing process that involves the production of parts by injecting molten material into a mold. This production method is popularly used in mass-production processes where the same part is made thousands of times in succession. How is it done? The mold is customized during tooling, which gives the shape of the part. As a result, it can create numerous identical and dimensionally consistent pieces, even on parts with complex designs.
When used to mass fabricate plastic parts, the process is known as plastic injection molding. In this case, the process involves an injection of molten plastic material into the mold, which cools and solidifies to its final form. Plastic injection molding is ideal for manufacturing high volumes of plastic products, which serves many industries and individuals.
Parts and products produced with this method are, for example, bottle caps, automotive parts and components, toys, one-piece chairs and small tables, mechanical parts, and many other plastic products.
But let’s take a closer look at the advantages of this type of production.
#1 Ability to produce detailed and complex parts with high precision
Injection molding is excellent for manufacturing highly complex and detailed plastic parts in large volumes with nearly no deviation. That is because it easily integrates with computer-aided design. Hence, it relies on comprehensive data collection and analysis techniques at the center of scientific molding and the engineers trained in the process.
Furthermore, plastic injection molding allows you to incorporate more features at minimal tolerances than other methods. Injection molders can complete designs accurately to within +/- .001 inches. These measurements are possible and are also repeatable across production runs and equipment.
#2 Efficiency and speed
Injection molding has a high production output rate, is cost-effective, and fast, making it the most efficient form of molding. Cycle times during this process that can be as low as 10 seconds, combined with the high quality of molds, mean a lot of products within a limited time frame.
That implies that this method generates excellent profit margins. In addition, implementing techniques like greater upfront focus on design to minimize problems later on and incorporating value-added services to combine production process steps can streamline time and cost burdens.
#3 Strenght and stability
Today’s lightweight thermoplastics can resist even the harshest conditions, and for constructing complex injection-molded applications, there are many engineered materials to choose from. Furthermore, the plastic injection molding process uses filters to reduce the density of plastic that adds strength and stability to the molded part.
High-performance blends and hybrids can also be formulated to meet particular part requirements and characteristics. Naturally, a proper balance of design considerations and material selection, based on the set conditions for the end product, helps additionally address the need for strength and stability.
#4 High-output production and consistency
High-output production of complex plastic parts demands a consistent, repeatable process to achieve designs with tight tolerances. Injection molding can produce numerous identical parts with consistent form and dimensions because it repeatedly uses the same mold for each piece. This advantage is essential when product consistency and part reliability in high volume production is required.
#5 Great flexibility
Injection molding offers excellent flexibility:
- There are many materials nowadays in polymers, as there are many plastic resins. Moreover, injection molding can simultaneously use multiple types of plastics.
- It allows for custom color choices thanks to the multiple coloring techniques that are available for adding shades the plastics,
- With plastic injection molding processes, multiple finish appearances like smooth surface finish, matte, or even unique textures.
- Can meet specific project requirements.
#6 Waste reduction
Plastic pollution worldwide has gone up to a severe level. As a result, industrial manufacturing processes must secure that they go hand in hand with today’s environmental considerations. In this direction, plastic injection molding uses only the required plastics during the production process and does not leave substantial waste. Hence it produces much less waste than traditional techniques, such as, for example, the conventional machines that cut plastic pieces from larger blocks.
#7 Lower labor costs
The ability to produce parts in bulk with minimal time and high output ratio makes injection molding a highly efficient process in terms of cost. In addition, the molding equipment requires minimal supervision because the process is entirely automated, so it streamlines labor costs and dramatically reduces the risk of rework caused by part defects or human error, ultimately saving money.
Conclusion
To truly benefit plastic injection molding, manufacturers must look for quality materials and experienced custom injection molders that know how to maximize efficiency and overcome any design or process issues. Having the best equipment, materials, and know-how ultimately makes a difference in the costs and final quality.
Tech
The Importance of Cyber Hygiene: Tips from HelpRansomware Experts
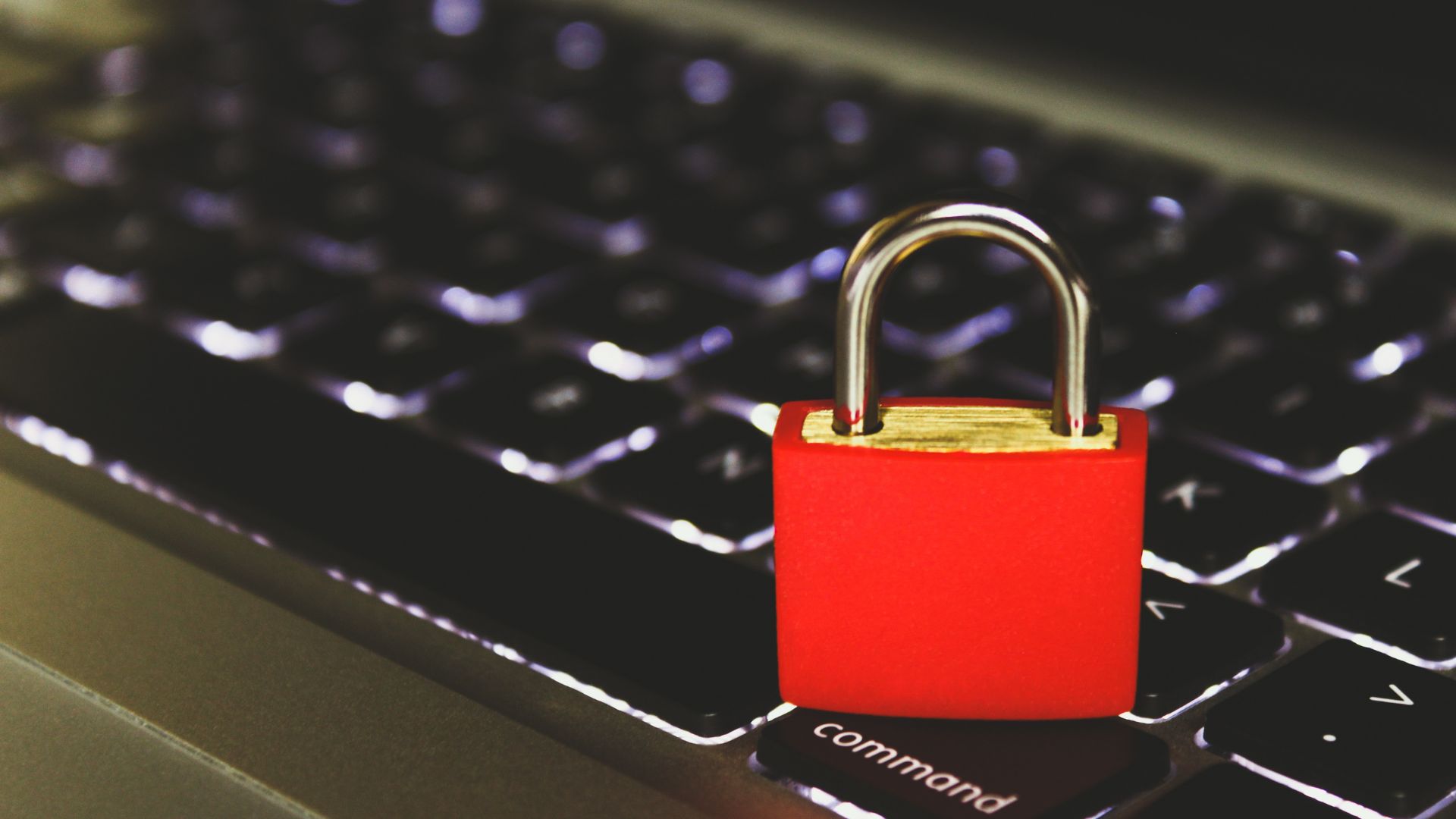
Byline: Katreen David
In the digital age, the adage “an ounce of prevention is worth a pound of cure” has never been more relevant.
For Juan Ricardo Palacio and Andrea Baggio of HelpRansomware, the battle against digital threats is a daily reality. Founded in response to the growing menace of ransomware, HelpRansomware has made it its mission to recover data while educating the public on the importance of cyber hygiene.
“Preventing a cyberattack before it happens is crucial. We can safeguard digital assets more effectively by nipping the threat in the bud through vigilant monitoring and proactive measures,” says Baggio.
The Growing Threat of Cybercrime
Cyber threats have become increasingly pervasive and sophisticated, impacting businesses and individuals alike. According to research, there are an estimated 2,000 cyberattacks per day globally. This equates to over 800,000 cyber crimes annually. In line with this, the worldwide cost of cybercrime is projected to reach the $23 trillion mark by 2027.
This alarming figure highlights the critical need for robust cybersecurity practices. HelpRansomware has responded to this challenge by accentuating the importance of preventive measures. “Our goal is to create a safer digital environment where cyber hygiene is as natural as brushing your teeth,” says Palacio.
Cyber Clean: Maintaining Digital Hygiene
HelpRansomware advocates for a proactive outlook on cybersecurity. It offers practical tips for maintaining good cyber hygiene, such as regularly updating software, using strong and unique passwords, developing risk management plans, and educating employees about phishing scams.
“Cyber hygiene is about taking small, consistent actions to protect your digital assets,” explains Palacio. “When we practice good cyber hygiene, the chances of cyber attacks occurring shrink significantly.”
Businesses can significantly reduce cyberattack vulnerability by integrating these practices into daily routines.
HelpRansomware’s Role in Promoting Cyber Hygiene
Beyond recovery services, HelpRansomware is dedicated to raising awareness and providing education on cybersecurity best practices. It conducts workshops and seminars to help organizations understand the importance of cyber hygiene. This unique initiative mirrors the company’s sincere efforts toward shielding the world from the dark side of the web.
“Education is the first line of defense against cyber threats,” emphasizes Baggio. “Francis Bacon’s famous quote will always ring true in every industry: ‘Knowledge is power’.”
HelpRansomware’s efforts are power moves across the board that help businesses recover from attacks. Its checkmate move, however, is its vision to build a culture of prevention that can safeguard against future threats.
In an era where cyber threats lurk around every unlikely corner of the internet, the importance of cyber hygiene cannot be overstated. Through its innovative solutions and educational initiatives, HelpRansomware is leading the pack in promoting better cybersecurity practices. “We believe that a well-informed and vigilant community can defeat cybercrime,” concludes Baggio.
HelpRansomware’s proactive stance on cyber hygiene is setting new standards in the industry. Through education and preventive practices, Andrea Baggio and Juan Ricardo Palacio are fortifying the digital community, making sure that future cyber threats are met with informed and resilient defenses. Cleanliness matters in both the tangible and digital world.
-
Tech4 years ago
Effuel Reviews (2021) – Effuel ECO OBD2 Saves Fuel, and Reduce Gas Cost? Effuel Customer Reviews
-
Tech6 years ago
Bosch Power Tools India Launches ‘Cordless Matlab Bosch’ Campaign to Demonstrate the Power of Cordless
-
Lifestyle6 years ago
Catholic Cases App brings Church’s Moral Teachings to Androids and iPhones
-
Lifestyle4 years ago
East Side Hype x Billionaire Boys Club. Hottest New Streetwear Releases in Utah.
-
Tech7 years ago
Cloud Buyers & Investors to Profit in the Future
-
Lifestyle5 years ago
The Midas of Cosmetic Dermatology: Dr. Simon Ourian
-
Health6 years ago
CBDistillery Review: Is it a scam?
-
Entertainment6 years ago
Avengers Endgame now Available on 123Movies for Download & Streaming for Free